Navy Contracts Mean Electric Boat Will Hire 14,000 Over Next 13 Years
By Julia Bergman
The Day
The Day
December 10, 2016
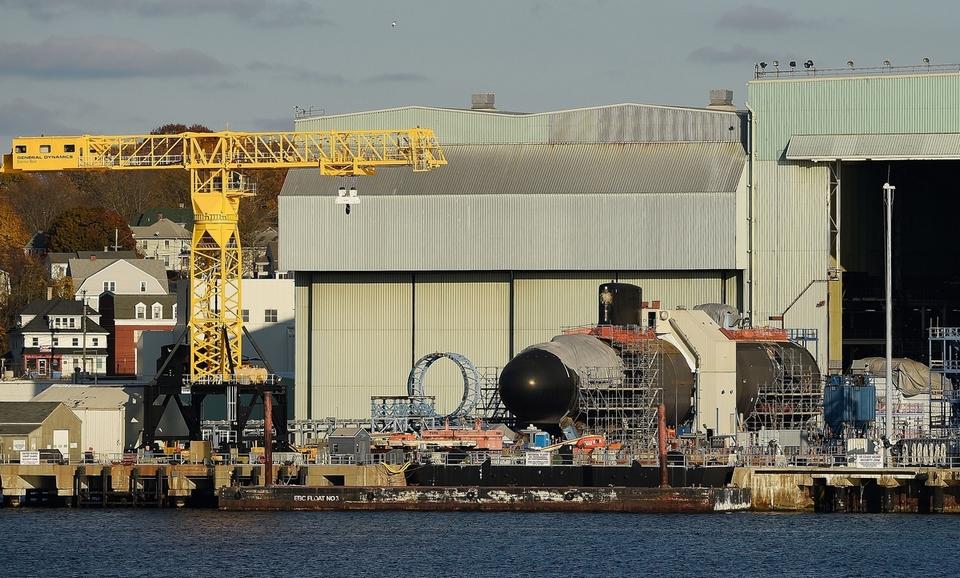
The hull of the Virginia-class attack submarine South Dakota (SSN 790) under construction
at General Dynamics Electric Boat in Groton Thursday, November 17, 2016. The South Dakota
is scheduled for launch in the summer of 2017 and commissioning in the summer of 2018.
South Dakota will be the 17th sub in the class and 7th in the Block III series of the class
featuring an improved sonar array and new vertical launch system in the bow.
(Sean D. Elliot/The Day)
Groton — For the best evidence of what billions of dollars in Navy contracts have done for Electric Boat, look no further than the submarine builder’s Groton shipyard.
Six different submarines are currently under construction there. Another is in for its “50,000 mile checkup.” And an eighth is undergoing a major overhaul.
Federal lawmakers, especially those whose districts stand to benefit from the defense jobs, have shown a renewed interest in submarines and their role to national security following a drop in submarine production after the Cold War and the prominence of other military policies in the period after Sept. 11.
It’s unclear exactly what kind of support submarines will get under a Donald Trump presidency. But Trump has said he wants a bigger Navy, specifically calling for 350 ships.
Strong congressional support for submarines in recent years has kept EB busy. The company and its partner Newport News Shipbuilding continue to build advanced attack submarines, funded by Congress at a rate of two-a-year for $5 billion. And the U.S. is poised to pay almost $100 billion for a new fleet of submarines that will carry ballistic missiles with nuclear warheads. EB, as the Navy’s prime contractor for the program, will carry out most of the work.
Already, 3,023 Electric Boat employees are working on the detailed design phase of the Columbia-class program, to develop a new fleet of 12 ballistic missile submarines to replace the current fleet of 14. Navy and other defense officials have called these new submarines the most survivable leg of the U.S.’ nuclear triad.
On the Virginia program, 6,687 employees are involved. And 722 employees are doing maintenance and modernization work. The company secured a $46 million contract to overhaul the USS Montpelier, which arrived at the shipyard in August and will be there for several years.
To keep up with its work, the company will hire 14,000 new employees over the next 13 years. Those employees will fill new positions and those being vacated by retirees and those who leave for other reasons. The burst in new hires will take EB from its workforce of 14,500 today to 18,000 in 2030.
This year alone, the company hired 1,600 new full-time employees. Another 800 received conditional job offers and are in the process of applying for a security clearance or awaiting that clearance.
The combination of an increased workload and an aging workforce — about 250 to 300 people retire each year — has prompted the large demand for skilled labor at EB.
While the engineering workforce has neared its peak, EB will continue to hire a larger number of shipyard personnel such as welders, machinists, and electricians. About 40 percent of this year’s new hires were tradespeople.
That’s why EB and the region’s technical high schools, community colleges and local workforce development organizations have spent the past two years building up manufacturing infrastructure last prominent in the 1980s. Training programs for welding and other trades are now in place to develop a stream of “better quality candidates coming in the door,” said Maura Dunn, head of human resources, in a recent interview in her Groton office overlooking the Thames River.
That “spade work” is starting to show, Dunn said.
EB has hired 82 percent of the 1,800 graduates from the training programs. Graduates have come to work with stronger foundational skills than their counterparts and are learning their trades faster, EB officials say.
Demand has been strong for the training program. More than 2,000 have registered on the program’s website and have followed up with from staff with the Connecticut Department of Labor, according to John Beauregard, president of the Eastern Connecticut Workforce Investment Board. The biggest challenge has been getting instructors, he said.
The students are a mix of those coming out of high school and adult career-changers, an important population to meet the volume of workers EB needs, Beauregard said. Beauregard’s group has secured $16 million in grants since 2011 to operate the programs, which are free for students. Nearly $10 million has been spent so far.
While EB has provided “in kind” donations such as developing the curriculum to ensure the students learn the company’s way of doing things, it has not invested any money in the program.
Internally, however, the company spends a lot of money to train new employees. Training a welder, for example, one of the more difficult trades to learn, costs the same as a year's tuition at the University of Connecticut, according to Stan Gwudz, EB's director of operations.
EB has spent millions to build so-called action learning centers, where new hires work in a model submarine hull to develop their trade and get used to working in tight quarters before moving on to work on a real submarine.
And early next year, the company plans to restart the apprentice programs for members of the design and carpenter unions.
Chris Gilbert, 22, was among the first graduates of the machinists class put on through the manufacturing pipeline. After applying to EB for a job as an outside machinist, the company recommended that Gilbert take the five-week class.
Gilbert said the job description on EB’s website was vague. But after going through the machinists class, he knew what to expect. In his first few weeks of on-the-job training, he was a little bored, he said, because he already knew much of the information. He is now teaching courses to those whose shoes he was in six months ago.
Despite the “good training” programs, hiring managers at EB are still struggling with “green labor,” or new hires, Gwudz said. “That’s the biggest concern for everybody,” he said.
“We have the 20-year-old with less than a year and we have the 60-plus with 40-plus years,” he said.
On top of that, employees are retiring from EB as fast as they are being hired, which is creating a void in the supervisor ranks. Developing young employees into managers will be an ongoing issue, said Dunn, the human resources vice president.
Still, the outlook is bright for the young folks there, Gwudz said, just as it was 43 years ago when he was starting at the company.
"They told me I'd be able to retire here no problem," he said.
Despite the good news for submarine manufacturing, southeastern Connecticut is still struggling to recover from the economic recession. Numbers released in November by the Department of Labor showed that the Norwich-New London area, which includes Westerly, lost 300 jobs over the last year. Economists have said layoffs at the two casinos have hindered job recovery in the area.
At a recent roundtable hosted by the Greater Norwich Area Chamber of Commerce, local business owners expressed frustrations about slow bureaucracy and a lack of trades help.